Semiconductor Processes and Products
Take Advanced Packaging to a completely new level
As functionality and reliability of electronic devices progress, requiring changes in systems development and integration, materials, chemicals and auxiliaries are undergoing significant adaptions in performance, cost-efficiency and reliability.
In order to respond to such needs, Umicore´s business unit Electroplating have partnered with SHINHAO Materials to provide innovative patented additives* for copper electroplating into the advanced packaging industry. SHINHAO´s modular additive system IntraCu®* embodies an integral part of our joint product offering. It is manufactured in state-of-the-art clean room environment to meet quality standards of the semiconductor industry. Several sub-products address particular properties and needs. Umicore´s Copper(II)oxide and Anode and Cathode solutions for ECD equipment are complementing our product offering and underline our competency in the segment of advanced packaging.
To complete our portfolio in the area of semiconductor processes, our Thin Film Products business line is at your disposal. They successfully develop, manufacture and supply high-quality evaporation materials and sputtering targets for thin film applications in the fields of advanced packaging, compounds, microsystems and silicon front-end segments.

Choose where you want to navigate or scroll down for the entire content:

Our modular additives are designed to meet the highest requirements of the semiconductor industry in advanced packaging and offer the foundation for depositing customized material properties e.g. for Microbumps in IC packages, RDL in wafer level packaging and Pillar in flip-chip packaging.

IntraCu® SC-1*
IntraCu® SC-1* System provides customers the opportunity to make products that require thermal and mechanical stability in future, so that fine lines/structures will not break during subsequent packaging and assembly operations. In addition, it offers a lower cost alternative for copper to copper direct bonding due to its signature flat topography. Furthermore, its submicron surface roughness and etch-resistant nature is a great advantage in PLP applications in addition to wafer level packaging.

- Fine line RDL (< 2 µm)
- Cu-to-Cu direct bonding

- Bamboo-like structure
- Matte Cu, Ra < 0.2 µm
- Flat topography
- Stable tensile strength
- Resistant to grain growth
- Resistant to etching
IntraCu® SC-2*
IntraCu® SC-2* System provide customers the opportunity to reduce total cost of ownership by extending the process window. In addition, it is a true 2in1 procedure that produces no or only a small number of Kirkendall-voids (KV-less). The system is a drop-in replacement for current POR offerings.

- 2-in-1 bright Cu (Cu pillar and RDL)
- 2-in-1 with KV-less requirement

- Bright Cu, Ra < 0.03 µm
- ±50% process window for Cu pillar and RDL
- Total in-film organics < 11 ppm
- Excellent KV-less performance


Umicore copper oxide high purity metal oxide powder are developed, manufactured and quality tested in accordance with the demanding requirements of the semiconductor advanced packaging industry. In combination with ancosys DMR® concept (Direct Metal Replenishment) clean room usage is possible enabling lower cost of ownership for Cu replenishment along with a boost in performance of the electrolyte through higher Cu concentrations.

No VMS Needed
- H2SO4 concentration remaining consistent. Stable electrolyte volume, feed and bleed not needed
- Several grades (4N, Packaging)
- Full traceability, only one source for Cu
Cost Efficiency
- Reduction tool down time, supporting maintenance-free plating chambers
- 50% lower cost per kg Cu compared with VMS
- 15% higher speed through higher Cu2+ (60g/l i/o 50g/l)


Insoluble anodes are proven to help increase process efficiency, reduce process costs, environmental impact and process control efforts in plating tools for advanced packaging. The key differentation of Umicore´s PLATINODE® is the unique layer performance due to the manufacturing method using a molten salt electrolyte allowing ultra-high purity, low porosity and best ductility even at high Pt layer thicknesses.
- Function: providing best-in-class ductility and chemical resistance due to unique HTE™ coating of electrode
- Customized designs, contact materials and coatings
- Fully integrated production and clean room packaging: Built-to-Order or series
- Insoluble anodes and cathodes in qualification for several WLP/PLP ECD Tools
PLATINODE® SC PtTi
- Molten salt deposited Pt on Ti substrate
- Developed for high ASD, predictable lifetime and outmost current distribution accuracy
- Pt thickness can be measured / correlated to lifetime
PLATINODE® SC MMO
- Developed for low organic consumption
- End of lifetime characterized by end of electrocatalytic function and wear rate
- Thickness cannot be measured / correlated to lifetime




Competent advice and technical service right from the start
For example, we offer an all-encompassing consultation in advance. We discuss with you the economic conditions for a transparent profitability calculation tailored to your needs. We also clarify specific details in your process in advance to create the most efficient process possible. On this basis you should be able to make a well-founded decision for or against our products.
Of course, we are also available to support you at any time after successful integration of the products - if desired, we can also be on site worldwide.
We are looking forward to get in contact with you
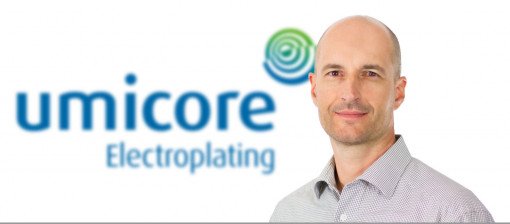
* Not available in Europe